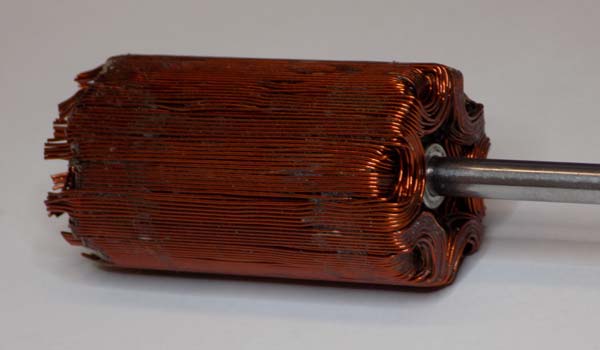
The Weller Technology
is an innovative and internationally patented process for the manufacturing of rotating electrical machines.
Technical description
Method of producing rotating electrical machines
Experts in the field are familar with the latest technology and mode of operation and the manufacturing processes of electric motors, thus the following description is only intended to explain the new process.
When developing electric motors, the main objectives are the following:
1.
2.
3.
The final assembly should be uncomplicated and require only a few work steps
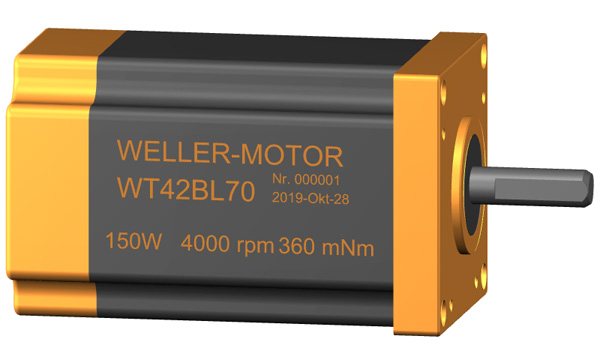
Ideally, the wires of the motor coil should be drawn straight across the magnetic field, the winding heads should be kept as short as possible and it should be possible to produce all of the segments one after the other as one piece.
We have managed to create this simple and effective production method with the new process.
On the prefabricated anchor, flanged washers with a slightly enlarged outer diameter and axle hole are attached to the ends. The armature (rotor) must have a homogeneous surface, because it will be used again later as a rolling tool.
The motor winding with the selected individual coils is now wound homogeneously in layers over the two flanged plates and the armature.
To strengthen the coils immediately or afterwards, baking enamel wire and suitable auxiliary tools such as placeholders for coil segmentation are used.
Once this working process has been completed, the armature can no longer move inwards or outwards due to the bulging of the coil wires which makes a formatting process necessary.
The entire unit, the motor coil with armature, is inserted into a slightly larger tube over the length of the coil. This serves as an abutment for the “motor spool formatting” step.
For this purpose, an eccentric rotational movement is applied externally to the armature axis and the armature core runs like a roller on the inner diameter of the motor coil, so that it is pressed against the abutment to its final dimension. This step involves heating the selfbonding enamel wire of the motor coil by applying current.
The eccentric stroke of the moving armature is then set to the intended air gap.
Following the formatting process described, the bearings can be mounted on the motor shaft. The armature can now rotate freely in the very precise air gap. The motor is ready after the completion programme has been finished with the remaining components. The drawing set provided is a clear illustration of the principles of the invention. This process can be used in a wide range of designs, for example air-coil armature motors with slip ring body or commutation, brushless motors with fixed stator and magnetised armature, reluctance motors, squirrel-cage motors, especially in mains operation, or external rotors.